I am working on fitting an ebike kit to my MTB. The kit is based on a 48V 1000W non-geared rear wheel hub motor. The MTB has an aluminium alloy frame (including dropouts).
During my research on this project, many articles recommended that the axel of the hub motor be fitted with a torque arm, particularly on aluminium alloy framed bikes. This is to help prevent the dropout lugs from breaking due to the torque applied to the lugs by the hub-motor axel.
Being a mechanical engineer, this got my inquisitive juices flowing. I decided to calculate how much torque my existing aluminium alloy dropout lug could take before failure. The result surprised me. My dropout lugs could theoretically take about 150N.m of torque each side (or 300N.m total) before failure. This is well above the maximum torque that most hub motors can apply.
This then got me thinking as to why dropout lugs were failing at much lower torque loads. The answer lay in the design of the existing dropout lugs and the hub-motor axel.
In the picture below, figure 1 shows a typical dropout log arrangement and the cross-section of a typical hub-motor axel. Due to the shape the axel, it cannot fully seat into the shape of the lug cut-out. The sharp shoulder on the axel between the flat and the threaded portion sits at the top of the half-round cut-out. This is shown in figure 2.
Any vertical load on the axel (and there is plenty when riding) will tend to move the steel axel further up into the aluminium alloy lug out-out forcing the sharp axel shoulder into the aluminium alloy. See figure 3.
These notches create a stress raiser in the aluminium allow that greatly reduces the strength of the dropout lugs against a torque load. See figure 4. Thus the cause of dropout lugs breaking well below their design limit.
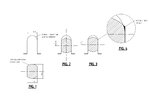
During my research on this project, many articles recommended that the axel of the hub motor be fitted with a torque arm, particularly on aluminium alloy framed bikes. This is to help prevent the dropout lugs from breaking due to the torque applied to the lugs by the hub-motor axel.
Being a mechanical engineer, this got my inquisitive juices flowing. I decided to calculate how much torque my existing aluminium alloy dropout lug could take before failure. The result surprised me. My dropout lugs could theoretically take about 150N.m of torque each side (or 300N.m total) before failure. This is well above the maximum torque that most hub motors can apply.
This then got me thinking as to why dropout lugs were failing at much lower torque loads. The answer lay in the design of the existing dropout lugs and the hub-motor axel.
In the picture below, figure 1 shows a typical dropout log arrangement and the cross-section of a typical hub-motor axel. Due to the shape the axel, it cannot fully seat into the shape of the lug cut-out. The sharp shoulder on the axel between the flat and the threaded portion sits at the top of the half-round cut-out. This is shown in figure 2.
Any vertical load on the axel (and there is plenty when riding) will tend to move the steel axel further up into the aluminium alloy lug out-out forcing the sharp axel shoulder into the aluminium alloy. See figure 3.
These notches create a stress raiser in the aluminium allow that greatly reduces the strength of the dropout lugs against a torque load. See figure 4. Thus the cause of dropout lugs breaking well below their design limit.
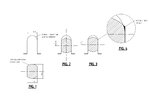