Hello
I have a diy battery ICR18650-26F 13S7P 48V 18Ah (see how it builded, tests https://www.instagram.com/explore/tags/electric_bike_apache_log/ )
I charged it with a standard 54V4A charger, but the shutdown happened ahead of time, as it turned out one parallel had charged up to 4.2V earlier than the others, the other parallels only charged up to 3.98V. This is sad, rather, either the marriage-cells or incompatible internal resistances, something else (I did not test each cell for capacity, current output and internal resistance, even 91pcs!).
While the necessary equipment is going to test the cells, I thought about the individual charging of each cell ...
It sounds crazy, but it ensures that each cell is charged up to 99%.
First of all, I looked on the Internet, maybe someone has already done this .... but did not find in the subject of electric bicycles.
Future changes in the current battery:
0) Increase the capacity to 31А - 13S12Р (156 cells 18650) 1.23$/pcs
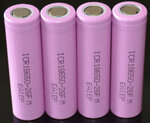
1) For each cell, connect a 2P3T slide-switch (3А250В, 6А125В should be enough for 2-4A cells) 0.09$/pcs
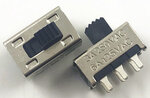
2) For each cell, connect a charging / protection module based on TP4056 (5V 1A) to the switch 0.2$/pcs
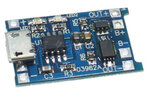
3) For each TP4056 connect diod shotki 1N5822 to reduce charge voltage up to 4.1-4.15V for increase cycles charge/discharge 0.02$/pcs
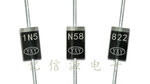
3) Optionally fuse 250V2A to each cell 0.015$/pcs
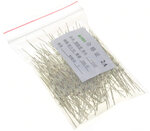
4) Approximately 0.8m of wire for each cell-charger&diodshotki-slideswitch 0.11$/m
For power supply of charging modules, power units S-400-5 (5В80А 400W) 2pcs are ordered, this should be enough for 140-160 TP4056.
Total: 156 switches ... 156 TP4056 chargers, 156 diodes 1N5822, 156 fuses, about 120m of wire (I don't know how it all fits in the frame of the bicycle but fire in the eyes burns with a green flame
)
After all the connections, I will have two charges:
1) Standard 54V4A - system plugin
2) Per-cell charger - switch system
I think on the first charge at all as well - just connect via the XT60 plug or any other convenient plug.
Per-cell charger:
1) Open the battery box
2) Disable the cable to the regular bms (just protection from the human factor)
3) Switch all 156 switches to the charging position
4) Connect the power supply of TP4056 through 2 power supply units.
5) After charging (all 156 TP4056 LEDs should be lit), toggle the switches
6) Connect cable to bms
7) Close the battery box
What do you think about this? What can be done easier? Did someone do something like that?
Sorry if the text looks strange - translate google.
I have a diy battery ICR18650-26F 13S7P 48V 18Ah (see how it builded, tests https://www.instagram.com/explore/tags/electric_bike_apache_log/ )
I charged it with a standard 54V4A charger, but the shutdown happened ahead of time, as it turned out one parallel had charged up to 4.2V earlier than the others, the other parallels only charged up to 3.98V. This is sad, rather, either the marriage-cells or incompatible internal resistances, something else (I did not test each cell for capacity, current output and internal resistance, even 91pcs!).
While the necessary equipment is going to test the cells, I thought about the individual charging of each cell ...
It sounds crazy, but it ensures that each cell is charged up to 99%.
First of all, I looked on the Internet, maybe someone has already done this .... but did not find in the subject of electric bicycles.
Future changes in the current battery:
0) Increase the capacity to 31А - 13S12Р (156 cells 18650) 1.23$/pcs
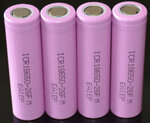
1) For each cell, connect a 2P3T slide-switch (3А250В, 6А125В should be enough for 2-4A cells) 0.09$/pcs
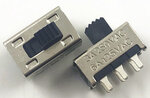
2) For each cell, connect a charging / protection module based on TP4056 (5V 1A) to the switch 0.2$/pcs
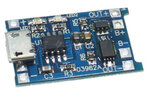
3) For each TP4056 connect diod shotki 1N5822 to reduce charge voltage up to 4.1-4.15V for increase cycles charge/discharge 0.02$/pcs
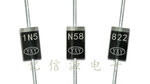
3) Optionally fuse 250V2A to each cell 0.015$/pcs
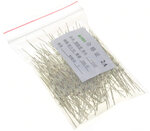
4) Approximately 0.8m of wire for each cell-charger&diodshotki-slideswitch 0.11$/m
For power supply of charging modules, power units S-400-5 (5В80А 400W) 2pcs are ordered, this should be enough for 140-160 TP4056.
Total: 156 switches ... 156 TP4056 chargers, 156 diodes 1N5822, 156 fuses, about 120m of wire (I don't know how it all fits in the frame of the bicycle but fire in the eyes burns with a green flame
After all the connections, I will have two charges:
1) Standard 54V4A - system plugin
2) Per-cell charger - switch system
I think on the first charge at all as well - just connect via the XT60 plug or any other convenient plug.
Per-cell charger:
1) Open the battery box
2) Disable the cable to the regular bms (just protection from the human factor)
3) Switch all 156 switches to the charging position
4) Connect the power supply of TP4056 through 2 power supply units.
5) After charging (all 156 TP4056 LEDs should be lit), toggle the switches
6) Connect cable to bms
7) Close the battery box
What do you think about this? What can be done easier? Did someone do something like that?
Sorry if the text looks strange - translate google.
Last edited: